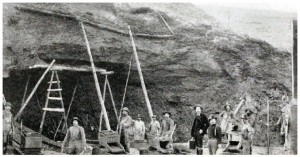
Canada is one of the world’s leading mining nations. From humble beginnings with small-scale coal mining on Cape Breton Island, N.S., 350 years ago, there are now more than 1,100 mining and exploration projects operating today.
Canada produces more than 60 minerals and metals. The country ranks No. 1 in the world in potash and uranium production. It is the world’s third-largest producer of diamonds, accounting for 14 percent of the global market by value and is in the top five in output of nickel, cobalt, cadmium, zinc, salt and molybdenum.
Canada and mining go hand in hand
The mining industry is an integral part of the Canadian economy. Its activities opened up the vast Canadian wilderness and today 115 communities owe their existence to it. The sector generated $54 billion in 2014, employed more than 383,000 people and paid more than $7 billion to government in taxes and royalties. A further $2 billion a year is paid in income taxes by its employees, who, at an average annual income of $110,000, earn more than twice the average wage of construction workers.
Mineral and metal product shipments contribute up to 60 percent of Canada’s rail freight revenues and as much as 75 percent of Canadian ocean port tonnage. In the record year 2011, mineral exports were valued at $101.9 billion, 20 percent of the value of Canadian goods exports. According to Statistics Canada, the GDP ”multiplier effect” for the mining sector is 0.88, meaning for each $1 million of GDP directly attributable to mining activity, $880,000 of additional GDP is created.
As a reflection of Canada’s dominant position in mining, the 83-year-old Prospectors and Developers Association of Canada (PDAC) hosts the world’s largest gathering of mining professionals each year in Toronto. In 2015, PDAC’s convention, trade show and investors exchange was attended by 23,578 people from more than 120 countries. The investors exchange had 480 exhibitors, mostly junior exploration companies, but also a number of major mining companies, mid-sized producers and prospectors seeking to attract investment and joint venture partners for their domestic and international mineral prospects. The trade show portion had 500 exhibitors showcasing mining technology, products, services and mining jurisdictions from around the world.
What is it about Canada and mining?
What makes Canada the world’s leading mining country? Is it simply because of its rich mineral endowment? The answer is a simple “No”: The U.S., Latin America, China, Russia, Australia and Africa all have superb endowments. The answer to the question, “What is it about Canada and hockey?” is pretty much the same.
“One of the reasons Canada has out-performed a lot of the Organization for Economic Co-operation and Development countries, certainly the G8, [is] our energy and mining prowess,” states Pierre Gratton, president of the Mining Association of Canada, in its publication, Facts and Figures 2012. “And now people are taking a hard look at what it is about Canada and mining and they are going beyond the actual production numbers to see this whole other part of the mining ecosystem we have built in this country.”
Today, the Canadian industry is a two-tiered system. A large number of “junior” companies that raise their own money on the stock market, from individual savvy investors or through joint ventures with other juniors, undertake nearly all of the high-risk, grassroots searches for new deposits and revisit abandoned former mining projects looking for extensions to and hidden deposits near these mines.
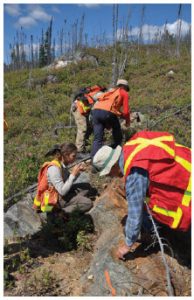
Canada’s role in global mining development
Senior mining companies are the minerals and metals producers, and their names tend to be well known to the public: Iron Ore Company of Canada, Barrick Gold Corporation, Xstrata (formerly Falconbridge) and Potash Corporation of Saskatchewan are a few of the giants. The two tiers interact when a significant discovery is made by a junior, with the senior company generally buying the project from the junior, the latter paid in cash, shares in the senior company and a royalty of a few percent on production. On occasion, with an exceptional deposit, a junior can get financial backing to go all the way to production and join the senior ranks.
The two-tiered system evolved from a largely unitary setup, whereby major mining companies did it all, including maintaining an exploration division to search for new deposits. Such companies, funded from their own treasury, were more risk averse, bureaucratic and, during downturns in the economy, cut back drastically or discontinued exploration altogether. The time it takes to put a proven ore deposit into production is five to 10 years, so the layoffs invariably caused boom and bust cycles in metal pricing and the inventory of mineable deposits varied, resulting in a most inefficient system.
The seeds for the development of junior mining (exploration) companies was the age-old fraternity of individual rugged prospectors, who went where they pleased, tramping the wilderness and breaking rocks everywhere. In the early days, most of the major mining districts in Canada were found by such individuals. It is no accident that the Prospectors and Developers Association of Canada bears this somewhat archaic name. The association was formed to assist prospectors, through lobbying efforts to educate the government on their importance to the Canadian economy, to obtain modest financial assistance and favourable tax treatment for their members, provide courses in rocks, minerals and geology and centralize advocacy on Canadian and provincial mining policy and regulations.
In this encouraging atmosphere, junior companies began to form in the 1960s, headed by professional geologists, who often had started their careers as employees of former exploration departments of senior mining firms. They put plans together, wrote a prospectus suitable for acceptance for listing by the Toronto Stock Exchange and began issuing shares for financing. A new era of scientific exploration brought quick success. With it, the senior mining sector virtually ceded exploration to the juniors
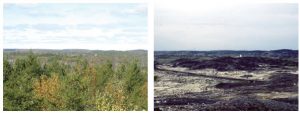
This enhancement in productivity was given a huge boost by the creation of “flow-through shares” by the federal government in its Mineral Exploration Tax Credit (METC), which attracted more investment to the junior exploration sector. The tax credit allows investors to purchase shares of a qualified company, deduct 100 percent of the cost of the shares from their taxable income and, in addition, claim a 15 percent tax credit on the investment. The new industry structure and this particular government initiative made Canada the No. 1 jurisdiction to raise mining exploration capital globally. Canadian mining regulations and policies became widely copied in mining countries around the world.
The evolution of the Canadian mining industry model had a global impact beyond just foreign adoption of Canadian policy. Not well known outside the industry, either at home or abroad, is Canada’s premier place in the development of global mining projects. Canadian-based mining and exploration companies listed on the Toronto Stock Exchange make up more than 1,200 of the world’s estimated 1,900 publicly traded firms, and own mining assets worth $234 billion. They also spend about 40 percent of the more than $10 billion global mining exploration budget on the search for and development of new mineable deposits. This level of effort and financing by Canadian companies makes Canada by far the world’s most important mining country.
Mining and the environment in perspective
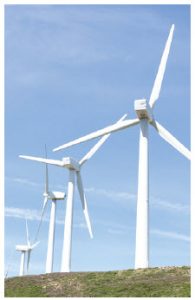
Negative environmental impact is usually the first thing that comes to mind when one mentions mining, and to be sure, this was not a romantic part of the Canadian mining story. Possibly the largest-scale environmental disaster connected to mining was caused by the open-air cordwood roasting of nickel ores in the Sudbury, Ont., area in the early years of the project.
“The roasting method was used by mining companies in Sudbury until 1929 as the primary means of separating minerals,” writes historian Krista McCracken, in an article in ActiveHistory.ca. “Fuelled by cordwood, these beds resulted in clouds of sulfur dioxide spreading from the beds at ground level. The roast beds have been blamed for much of the environmental destruction in Sudbury. However, it has also been argued that the later smelter technology also contributed to considerable environmental devastation by releasing sulfur dioxide into the atmosphere.
“The result of years of continuous mining and expulsion of associated pollutants resulted in approximately 7,000 lakes within 17,000 square kilometres being acidified, 20,000 hectares of barren land being created in which no vegetation grows and significant erosion has occurred, and 80,000 hectares of semi-barren land.”
It wasn’t until the 1960s that growing concern about the environment began to be voiced and regulations promulgated, and not just about the effects of mining. Smog in London, Los Angeles and other major cities of the world, pollution of the seas by bilge pumping, raw sewage, garbage dumping and chemical wastes from cities and industry, were, prior to the 1960s, not something humans thought they could or should do something about.
Captured in the photos below is a succinct summary of the efforts to right the wrongs of what occurred in the mining industry and, indeed, all other sectors of activity. In the 1960s and 1970s, government regulations were enacted and a re-greening program was started that involved neutralizing the acidic soils with limestone and the planting, to date, of more than nine million trees. The successful Sudbury re-greening effort is being used as a model for rehabilitation of the environment globally. An international example is the subject of a May 24, 2013 episode of CBC Radio’s Serving up the North: Sudbury biologist teaching Russians about re-greening.
Today, stringent environmental regulations for mining and mineral processing at federal and provincial levels require public stakeholder consultation, baseline studies by independent consultants who gather metrics on the flora, fauna and habitat, fish and other aquatic dwellers and plants, landscape, surface water and groundwater chemistry to serve as a threshold for measuring possible changes and the need for mitigation once mining activity starts. Monitoring also continues for a number of years after a mine is closed. A reclamation plan that returns the land to wilderness or alternate use by stakeholders is designed and funded in advance of starting the mine. The project is also subject to agreements with First Nations on lands covering traditional use areas, and includes training, employment and other benefits.
Canadian mining companies now are among the best in the world in terms of protecting the environment and reclamation. However, accidents do happen, as with any industry. The Mount Polley copper-gold mine tailings dam failure in northern B.C. in August 2014 was the largest of five Canadian accidents since 1960, according to “Chronology of major tailings dam failures.” Timely reporting is a matter of law and mitigation action is planned for in advance. Federal and provincial regulators take their work seriously and do their jobs responsibly. Mines can be shut down on same-day notice until any violation or accident is thoroughly mitigated.
We know that mining is essential to provide the raw materials needed for our human civilization. It is now pretty much agreed by all that it should be done safely and with respect for the environment. The Mining Association of Canada (MAC) has been most proactive in this area.
“The Canadian mining industry has made great strides in recent decades to minimize the environmental footprints of [its] operations and improving the reclamation of land. This progress has been driven by the actions of individual companies, government regulations and industry standards such as MAC’s Towards Sustainable Mining (TSM) initiative. One of TSM’s central goals is to minimize mining’s impact on the environment and biodiversity through all stages of the mining lifecycle, from exploration to mine closure. Companies are measured and publicly report their performance for several environmentally focused TSM protocols, including tailings management, energy use and greenhouse gas emissions management and biodiversity conservation management.”
Malthusian myth of mineral depletion
It isn’t news that mining supplies the mineral raw materials needed by society. However, does it not raise the question: What will we do when these finite resources have largely been mined? This apparent conundrum was first voiced and popularized in writings on population by Thomas Malthus, English cleric and economist, in the late 18th and early 19th Centuries.
“The power of population is indefinitely greater than the power in the earth to produce subsistence for man,” Malthus wrote.
In the 1860s, W. S. Jevons, another English economist, foresaw coming shortages of coal causing collapse of the Industrial Revolution.
The proposition of predicted shortages continues to have traction to this day in organizations such as the Club of Rome. The Club’s 1972 Limits to Growth, and later works, predict a Malthus-type collapse of society because of expectations of shortages of resources and food. Such thinking has a fatal flaw because it leaves out the single most important factor affecting such considerations: human ingenuity. It is the reason Malthus’s projection that growing cities would ultimately be buried in horse manure turned out to be unfounded.
The World Bank estimated the number of people living in absolute poverty in 2008 to be 1.29 billion. This means that today’s population, despite being double that of 1972 when Limits was published, is living much better and expanded food production has essentially made widespread famines in Asia a thing of the past. According to various demographers, population is expected to peak between 8.8 billion and 10 billion during the latter half of the 21st Century. The petri-dish model of human helplessness in a world of diminishing finite resources has been repeatedly discredited.
Will we have sufficient mineral materials to supply a world when the ultimate couple of billion citizens have joined us? An epigrammatic quote by Saudi oil minister Sheik Ahmed Zaki Yamani, in a 2005 New York Times article on peak oil answered the question this way:
“The Stone Age didn’t end for lack of stone, and the oil age will end long before the world runs out of oil.”
The supply of mineral materials is not simplistically a fixed stock slowly being drawn down toward zero. First, every tonne of material we have mined over the millenniums and put into finished products is still here on the surface of the Earth, except for the few tonnes we have sent to Mars and other parts of the solar system. Metal scrap has been recycled for a few thousand years because of its value. But we didn’t start husbanding our “used” resources intensively until the 1970s with proactive involvement of ordinary citizens in recycling a wide variety of materials. As a bonus, remanufacture with recycled materials saves up to 75 percent in energy, relative to the use of newly mined and refined resources.
Second, stretching resources to make things has been an important part of our progress in management of material needs. Starting in the latter half of the 20th Century, advances in engineering have continued to reduce the amount of material inputs into a product. Computers in the 1960s that took up an entire room couldn’t match the computing power of a laptop weighing less than a kilogram today and likely a fraction of a kilogram tomorrow.
Third, substitution of resources relieves pressure on any particular resource. The largest passenger aircraft in the world, the A380F Airbus, weighs 592 tonnes, fuelled and ready for takeoff. Carbon fibre-reinforced plastic is used extensively in the wings and an aluminum alloy-glass fibre laminate is used for the upper fuselage, largely replacing aluminum with ultra-strength lighter-weight substitutes. Automobiles and railway coaches, all the way down to a multitude of devices used by individuals every day, have similarly been transformed by abundant new age materials.
Fourth, new ore deposits of all the metals and minerals we use are being discovered by using technologies not thought about a generation ago. Remote sensing from satellites, computerized sensitive geophysical surveys — both ground-based and airborne — and ever-expanding geological knowledge are finding mineral resources we will be using for multitudes of generations into the future. For example, according to a U.S. Geological Survey assessment, remaining global resources of copper are estimated to be 3.5 billion metric tonnes and annual global production in 2013 was 20 million tonnes. Copper Facts estimates the total amount of copper mined globally since ancient times to be 557 million metric tonnes. There certainly is no imminent fear of running out of copper.
Rare earth and recycled metals
To obtain, refine and form mineral materials from the earth for our use and very survival is as much a must for humans as it has been since our hominid ancestors started digging almost three million years ago. However, hard lessons have been learned and continue to be learned about the care and attention that must be paid to minimizing damage to our environment. Regulations based on use of the best available abatement and mitigation technology in Canada, federal laws that require employment of the same technologies wherever Canadian companies operate abroad and the inexorable onward march of technology itself, give confidence that mining’s environmental, health and safety disasters of the past will become diminishingly few in the future.
In recent years, mining has become a “topping up” stream of materials used to manufacture products that are used, then discarded to be recycled back. Many manufacturers are making their products with the idea of having customers recycle them back to the supply chain instead of discarding them. Dell Computer Corporation is but one example.
Once merely part of the research chemist’s obscure Scrabble board of the elements, rare metals, particularly the 15 metals known as the rare earth elements, have been added to the engineer’s materials toolkit for the new technological age. “Going Green” with alternative energy had to depend on large-scale exploration, mining, processing and refining technologies to meet the rising demand for pure rare-earth metals for electricity-generating wind turbines, LED (light-emitting diodes) lighting, other low energy-consuming lamp technologies, laser generators, automobile and industrial process exhaust catalytic converters, colour phosphors for electronic devices, and many other everyday items.
These 15 metals: lanthanum, cerium, praseodymium, neodymium, samarium, europium, gadolinium, terbium, dysprosium, holmium, erbium, thulium, ytterbium, lutetium and yttrium, occur together in a variety of mineral species. Their chemical similarities made separation into individual pure metals challenging and their early uses were as unseparated alloys and compounds for de-oxidizing high-quality steels and making cigarette lighter flints and gas mantles for kerosene lamps. And it wasn’t until the 1960s and 1970s that threshold amounts could be made available for applications research.
Within the last 20 years, rare earth use has soared in environmental and health applications. Lanthanum-rich alloys with other rare earths are used for hydrogen storage batteries; cerium in ceramic dental compositions to replace amalgam fillings, auto exhaust catalysts and for scavenging toxic heavy metals in steel manufacture; praseodymium in medical CAT scan equipment; neodymium, samarium and dysprosium in high-intensity magnets for wind-turbine electrical generators, motors for electric and hybrid cars and computer disc drives; gadolinium in medical MRI technology; erbium in laser surgery technology; thulium in portable X-ray equipment; ytterbium to convert radiant energy (heat) to electricity; yttrium and europium in phosphors for the red colour in modern television, computer and cell phone screens. All of these also find use in a wide range of industrial, communications, space and other sectors.
Solar panels use high-purity silicon metal, gallium, boron, indium, selenium and tellurium. Silicon is at present the bulk photovoltaic converter because of its comparatively low cost. Gallium is used for space vehicle photovoltaics. A doubling of efficiency of conversion from solar to electricity could be achieved by substituting gallium for silicon and research has succeeded in reducing the film thickness of gallium required to one micron, compared to silicon’s 100 microns. This achievement has made possible next-generation versatile thin film, a flexible plastic solar-converter material. Lithium metal batteries, well known in computers, cell phones, watches, pacemakers, flashlights and the like, are now powering electric vehicles and finding use in energy storage — a technology that will solve the problem of gathering power from wind turbine and solar arrays to serve a stable electrical grid.
These developments have begun to forge a partnership from what has been a rocky relationship between miners and environmentalists. Mining companies now routinely employ environmental biologists and corporate governance specialists at the executive level.
Yana Amis has been president of a mining consulting firm for 17 years and is a mineral commodity economics researcher.